Rotating Head Cutoff Lathes
Are You Using the Right Tube Cutoff Equipment?
The Rotating-Head Tube Cutoff Lathe is a more advanced way to cut tubes, because the tube is held stationary for cut off and chamfering. This gives the lathe the ability to produce parts that are finished on both ends of the cut piece. There are built-in routines for grooves, bores and J-preps, so setups are fast and repeatable. These versatile cutoff machines eliminate secondary operations and reduce labor. And the automatic off-loading of the cut tubes is simpler and safer because the tubes aren't spinning.
- The tube is held stationary in two chucks, therefore, the tube does not spin during the lathe cutoff cycle.
- Conversely, the headstock spins while the cutting and chamfering tools move under servo control.
- This means both ends of the tube can be chamfered, grooved and bored in one setup.
- In addition, bowed or bent tubes can be processed (within limits).
- As a bonus, you get programmable setup for both product diameter and optimum cut lengths.
- Our automatic tube loading systems will accept full bundles, ensuring that you get continuous production.
What are the other most common methods used to automatically cut tube or pipe?
A Band Saw is the type of machine used most often to cut tubing, primarily because of the low initial cost and the simplicity of the equipment and the process. Some band saws can be equipped with automatic tube loaders, but most are loaded manually. While band saws can cut relatively quickly and can even cut several tubes at once, they have a few shortcomings.
- The band saw cutoff usually leaves a sharp burr that creates a handling hazard and can interfere with secondary operations.
- The band saw blade can flex and "wander", so the length of cut pieces can vary.
- Most bandsaws are manually loaded and unloaded, so labor is higher and overall production rates can be low.
A Cold Saw can also be used to cut pipe and tube, and this method of cutting produces a more precise tube end when compared to a band saw. However, when cutting tubular material instead of solid bar there is a problem with "chip recut", where the cutting chips get pinched between the blade and the material. This dulls the blade tips, shortens the blade life and can leave a rough tube end. Cold saws produce better cuts, but they have a few shortcomings as well:
- The quality of the cut may be good at first, but as the blade gets dull the cut quality gets worse and the blade must be replaced.
- Even with a sharp blade, there can be sharp edges that must be removed in a secondary de-burring operation.
- The cold saw blades are expensive, and although they can be sharpened, the performance of a sharpened blade rarely equals a new blade.
- Many cold saw machines lack the mass and rigidity needed to properly support the blade and workpiece that is essential to reduce harmonics.
A Laser is relatively new tube cutting method, with fiber lasers gaining in popularity. Although lasers can be used for straight cuts of tubing, the real benefit is the ability to produce more complex tubular parts. Lasers can cut holes, slots, notches and other features anywhere along the tube, and can cut square and rectangular shapes. Lasers can cut thin-wall relatively quickly and offer some special features, but there are a few drawbacks.
- The high temperature created by the laser causes the tube end to become brittle, and this can be a problem for secondary forming operations.
- Tube endfinishing and additional handling may be required to remove the heat-affected-zone.
- The laser process is not the best choice for cutting heavy-wall tube, especially if close tolerances and smooth surfaces are required.
- Laser machines are expensive to operate, with high cost of consumables and maintenance.
A Conventional Tubing Cut Off Lathe that rotates the tube is older technology, and there are many of these systems in use. Their primary applications are where threading or complex tube end profiling is required on one end of the tube. Some lathe cutoffs are equipped with automatic tube loaders and off-load systems, and some can include secondary maching stations. However, there are some limitations to consider, especially if the tubes are not perfectly straight.
- Because tubes are often bowed, any cutting process that rotates the tube will cause vibration.
- Vibration can be so severe that it affects cutting, wears the equipment and creates a safety hazard.
- The trailing end of the tube cannot be further machined after cutoff.
- A secondary operation or re-chucking is required to completely endfinish a tube.
We've been tackling tough applications and delivering innovative, dependable tube automatic tube cutting machines and special production systems since 1972.
Hautau Technology sets the standard for the industry because of the way we apply it to solve unique customer requirements. One Hautau Rotating Head Cutoff Lathe does it all. You get unmatched capability on a full range of tubing wall thicknesses, plus quick changeover. You can get a customized, turnkey system and be assured of reliable production for decades.
Exhaust Components
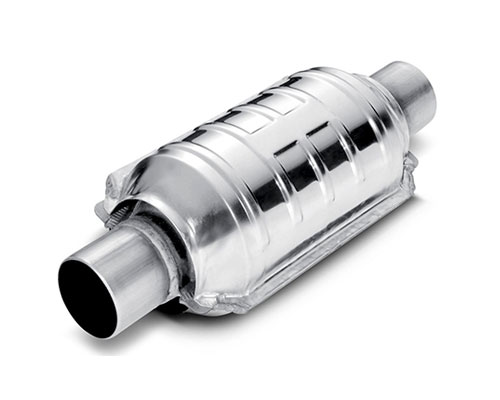
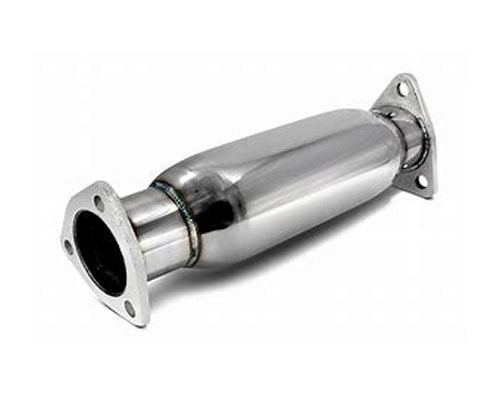
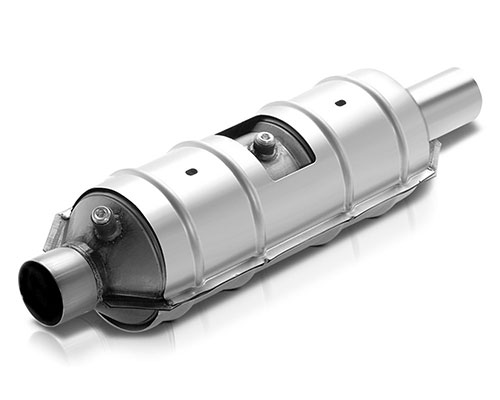
Hydraulic cylinder tubes
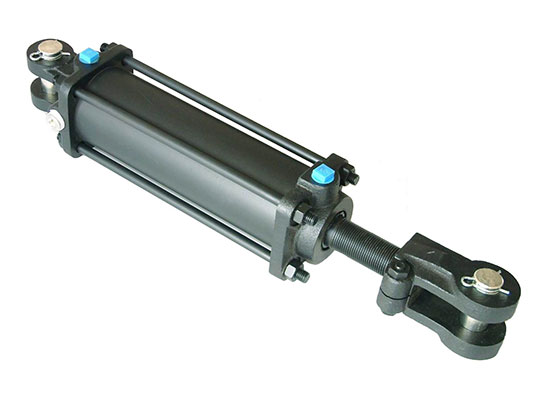
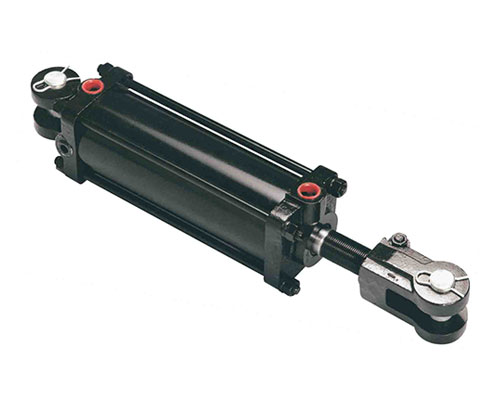
Gear and bearing Blanks
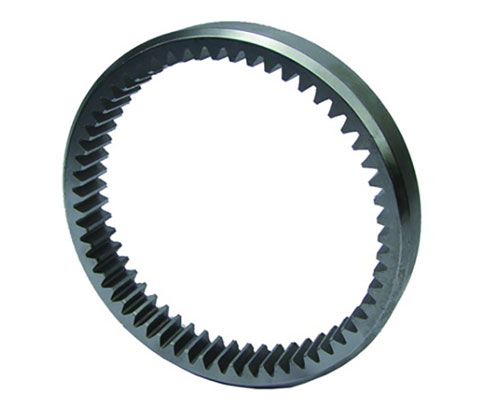
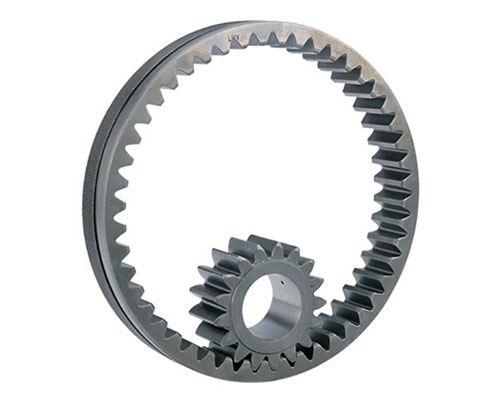
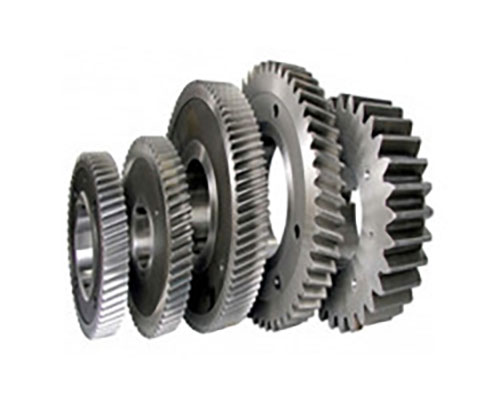
driveshafts and axle tubes
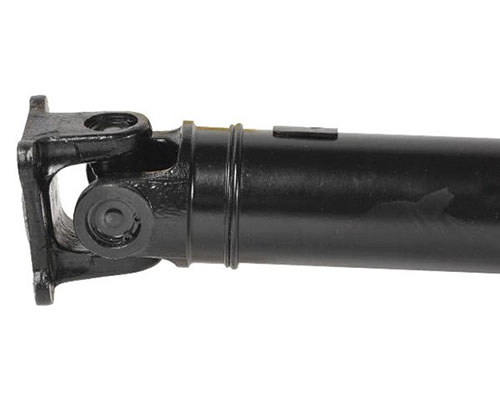
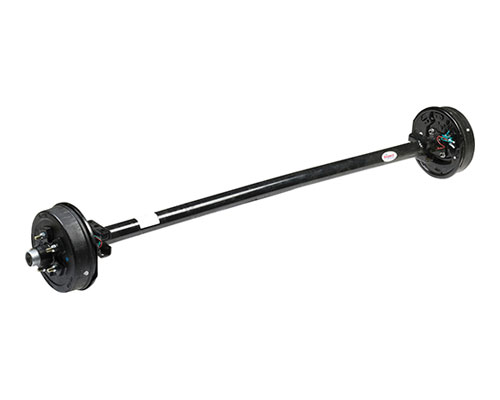
Conveyor idlers, rollers and pulleys
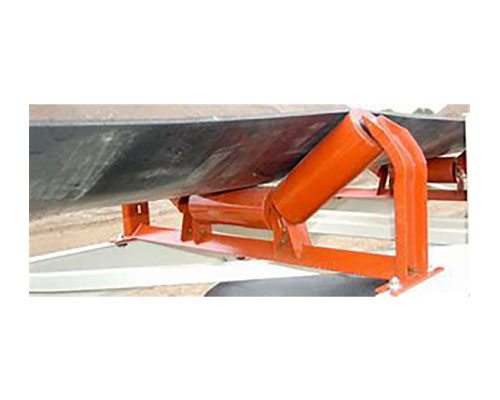
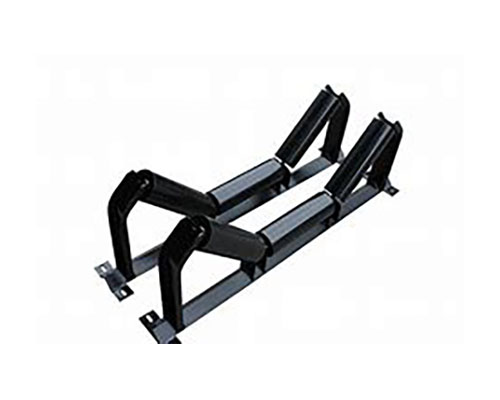
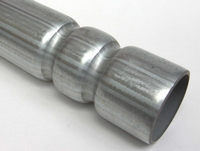